HVLP vs Airless Paint Sprayers
When choosing between HVLP (High-Volume Low-Pressure) and airless paint sprayers, professional painters must weigh several key factors. The HVLP vs airless debate isn’t about which system is better overall, but rather which is most suitable for specific applications and work environments. After years of professional cabinet finishing experience, we’ve found that airless sprayers are superior for high-volume cabinet production, while HVLP systems have their place in certain specialized applications.
Production Efficiency: Why We Choose Airless for Cabinet Production
In our high-capacity cabinet refinishing facility, we’ve found airless sprayers to be the clear winner for production efficiency. The key advantages include:
The ability to spray continuously from large paint containers eliminates the constant refilling required with HVLP cup systems. This alone significantly reduces downtime and increases daily production capacity. When you’re finishing hundreds of cabinet doors daily, these time savings add up considerably.
Operator fatigue is notably reduced with airless systems. The spray gun is lighter without an attached paint cup, allowing our technicians to maintain consistent quality throughout long production shifts. This becomes particularly important during extensive cabinet projects where painters might be spraying for hours at a time.
Special Resource: The Cabinet Painting Marketing Blueprint
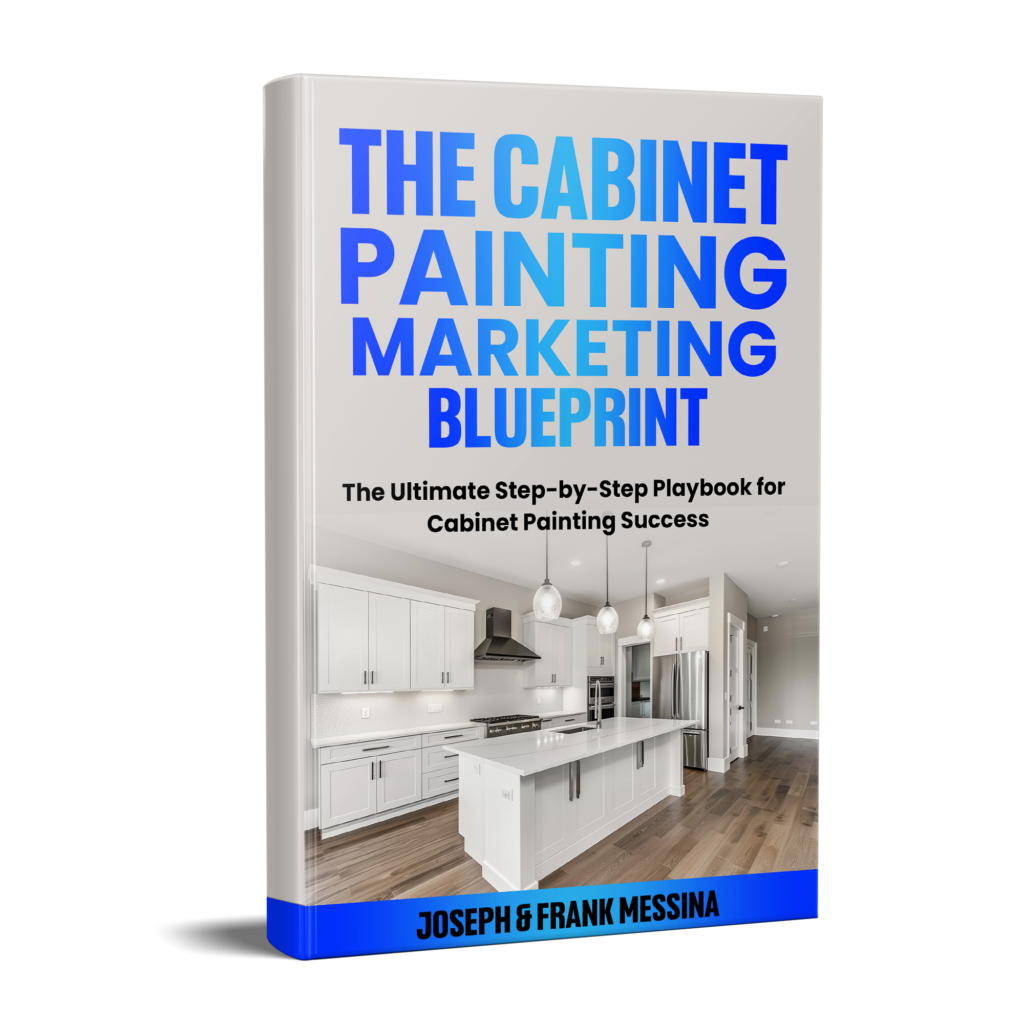
Do you want to land more high-paying kitchen cabinet painting jobs? Learn from the Cabinet Painting Bros who consistently land 300+ cabinet painting projects a year! Download the Cabinet Painting Marketing Blueprint, packed with proven strategies and insider tips to grow your painting business. Don’t miss out on this step-by-step guide to generating cabinet painting leads like a pro.
Material Handling and Application Speed
Airless systems excel at applying most cabinet-grade finishes without thinning. Their high-pressure operation (typically 2000-3000 PSI) effectively atomizes even heavier materials, resulting in:
- Faster application speeds
- Better coverage with fewer coats
- Consistent film build
- Excellent penetration into surface pores
HVLP systems, while precise, often require material thinning and multiple passes to achieve the same film build. This additional preparation time and slower application speed can significantly impact production schedules in a high-volume environment.
Finish Quality Considerations
While HVLP systems are often praised for their fine finish capabilities, modern airless equipment with proper tip selection can achieve comparable results. The key differences lie in:
Airless Advantages
- Faster building of mil thickness
- More consistent coverage on large surfaces
- Better penetration into wood grain
- Quicker production of smooth finishes
HVLP Benefits
- Excellent control for intricate details
- Minimal overspray in confined spaces
- Superior transfer efficiency
- Perfect for small, detailed projects
Practical Workplace Considerations
The choice between HVLP and airless often comes down to practical workplace factors:
Space and Setup Requirements
Airless systems require minimal setup time once properly configured. The ability to draw directly from paint containers streamlines the production process and reduces cleanup time. This efficiency is crucial in a production environment where time equals money.
HVLP systems typically need more frequent maintenance during use, primarily due to cup refilling and cleaning. While this might be acceptable for small projects, it becomes a significant bottleneck in high-volume operations.
Operator Experience and Training
Training requirements differ between the two systems:
Airless operators need to understand:
- Pressure settings and adjustment
- Tip selection and maintenance
- Proper spraying technique
- Safety procedures for high-pressure equipment
HVLP operators must focus on:
- Material viscosity adjustment
- Air pressure and flow settings
- Cup handling and maintenance
- Pattern control techniques
Cost Considerations
The investment analysis between HVLP and airless systems should consider:
Initial Investment
Both systems represent significant investments, but ongoing operational costs often differ more significantly than initial purchase prices.
Operational Costs
Airless systems typically offer lower per-project costs in production environments due to:
- Reduced labor time
- Lower material waste
- Faster project completion
- Less downtime for refilling
Maintenance Requirements
Regular maintenance is crucial for both systems but differs in focus:
Airless maintenance centers on:
- Pump maintenance
- Tip and filter cleaning
- Hose inspection
- Packing maintenance
HVLP maintenance requires:
- Regular cup cleaning
- Air cap maintenance
- Needle/nozzle care
- Turbine filter cleaning
HVLP vs. Airless Sprayers: What’s Better?
For high-volume cabinet finishing operations, airless sprayers provide clear advantages in production speed, operator comfort, and overall efficiency. While HVLP systems excel in certain specialized applications, the practical benefits of airless systems – particularly reduced operator fatigue and increased production speed – make them the optimal choice for professional cabinet finishing facilities.
The decision between HVLP and airless ultimately depends on your specific needs, but for high-production environments, airless systems consistently prove to be the more practical and efficient choice. Their ability to maintain high production rates while delivering excellent finish quality makes them indispensable in professional cabinet finishing operations.
Special Resource: The Cabinet Painting Marketing Blueprint
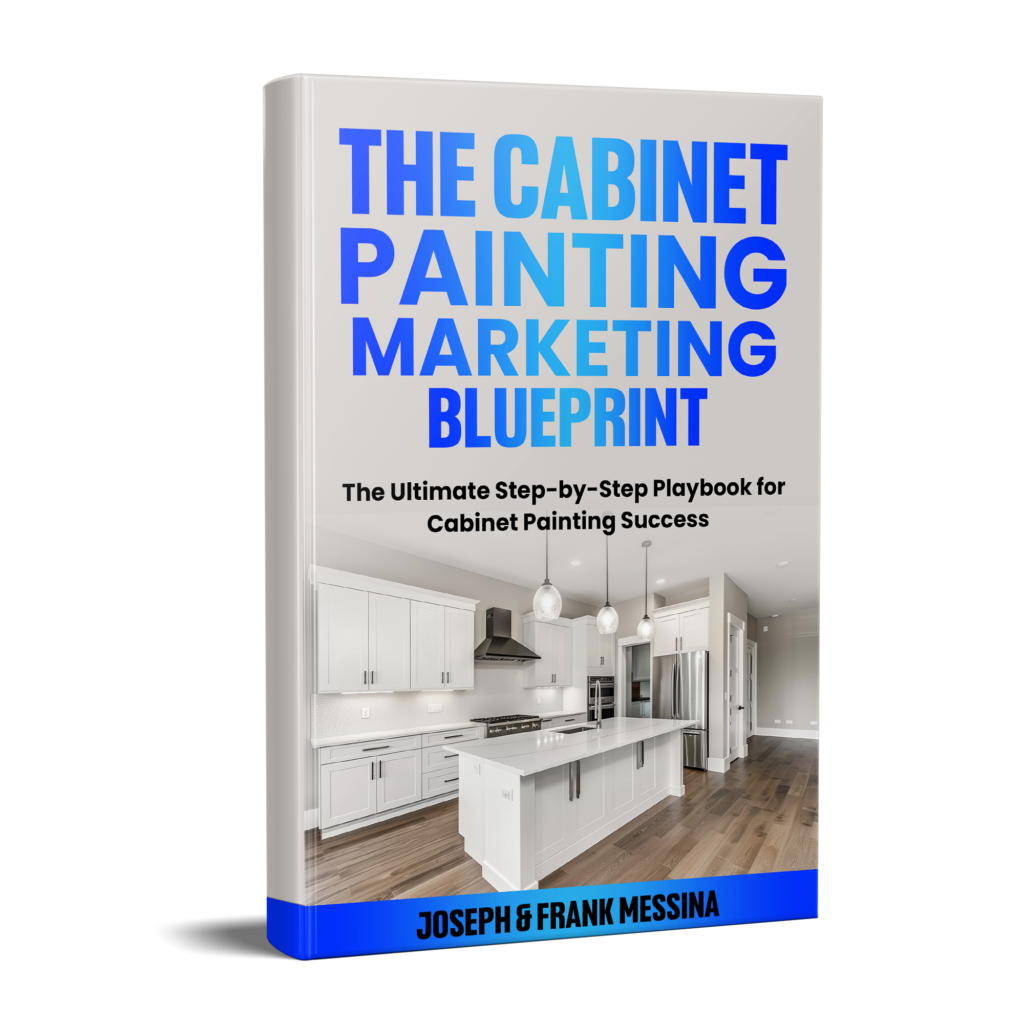
Do you want to land more high-paying kitchen cabinet painting jobs? Learn from the Cabinet Painting Bros who consistently land 300+ cabinet painting projects a year! Download the Cabinet Painting Marketing Blueprint, packed with proven strategies and insider tips to grow your painting business. Don’t miss out on this step-by-step guide to generating cabinet painting leads like a pro.